Maintaining high-quality standards is a top priority in construction due to its impact on a company’s financial health and reputation. Quality control is crucial, leading to repeat business and effective cost management. Conversely, subpar work can harm a company’s reputation, result in additional costs, and have various negative consequences.
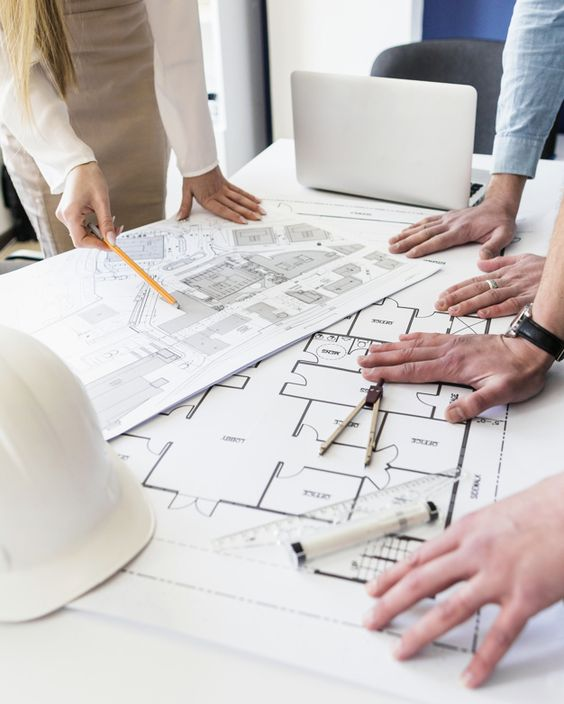
Low-quality work affects safety, communication, and resource utilization, wasting time and materials. Implementing proper quality control processes enhances project efficiency and fosters a culture of high expectations within the organization.
Defining Quality Control in Construction
A management system called construction quality control makes sure that project deliverables adhere to the rules and regulations set forth by the client. It includes a variety of standards, such as adherence to the project’s scope. In the end, the client, governing authorities, and EPA requirements determine quality.
Both quality control and quality assurance are crucial elements, with assurance establishing the standards for quality management and control concentrating on the processes and strategies to attain high quality. When quality-affecting elements are not correctly detected and managed, issues may occur. The goals of construction quality control are to address problems, produce superior outcomes, and foresee potential concerns.
Construction Quality Control Approaches
Quality control management in construction offers various approaches, each with its own advantages and disadvantages. ISO 9001, established by the International Organization for Standardization, includes standards related to engagement, customer focus, leadership, processes, improvement, evidence-based decisions, and relationship management.
There are four other major approaches:
Continuous Improvement: Emphasizes ongoing, incremental process enhancements based on customer feedback and internal analysis.
Kaizen: A philosophy of continuous improvement applied to quality control management, with all organization members seeking gradual improvements over time.
Six Sigma: Focuses on proactive issue identification and resolution through steps like Define, Measure, Analyze, Improve, and Control.
Lean Management: Prioritizes the elimination of waste and reduction of non-value-adding processes and materials for better customer and company value.
How to Ensure Construction Quality Control
Investing in construction projects carries significant financial risk due to common delays and disruptions that can lead to unexpected costs. To ensure quality in commercial projects, key considerations include thorough due diligence, risk assessment, transparent communication, clear legal agreements, adequate budgeting, regular inspections, professional project management, documentation, and continuous monitoring to address challenges and maintain quality.
Quality Assurance for Commercial Construction Buildings
Successful commercial construction projects rely on key themes, including clear communication, efficient planning, and effective coordination among various professionals. These elements are essential for driving the project towards successful execution
Communication Is Key
Construction projects that are successful and resilient must have effective communication to avoid errors, resource, time, and money waste. Prioritize team communication by educating the workforce on best practices, such as getting input from all participants, to ensure quality in commercial projects.
Effective communication is essential between designers and engineers as well as between contractors and other suppliers like plumbers and electricians. Team members’ confusion is decreased by minimizing industry jargon and putting an emphasis on clarity. The crew’s inquiries should be answered in detail by the project manager, who should be approachable.
Planning Before Procurement
The best way to organize a construction project is to prepare the building’s layout, design, and other specifics before beginning the procurement procedure. Using 3D modeling software, you can create your own facility. Sharing the design with other project participants will be simple.
Use Automation When Possible
Automation software can be used to streamline many of the complex intricacies of building planning. You may expedite processes like budgeting budgets, scheduling work hours, and filtering emails by using a variety of automation technologies.
Quality control during the construction process
In order to satisfy the client, it is crucial for the contractor to place a strong emphasis on quality control throughout the construction process. It’s beneficial to keep the client informed of the project’s development and solicit their input at each stage. Each day of construction must undergo a thorough examination for strong quality control.
Quality Materials & Equipment
High-quality tools and materials are used to construct high-quality structures. Contractors need to be cautious when dealing with dependable and trustworthy providers. Over time, using durable materials will cost less because there will be less need for replacement. To keep equipment in good functioning condition, it is advisable to perform routine inspections. Power tools that don’t function properly can be dangerous and harm the building.
Skilled & Experienced Workers
While new technologies can significantly improve construction, qualified and knowledgeable builders are also necessary for high-quality work. If the output frequently contains expensive faults, a construction company aiming to save money by hiring low-paid young starters won’t build a good reputation.
Aim for a Quality Structure with Level X Construction!
Spending time considering the specifics and surrounding oneself with construction experts are the greatest ways to ensure excellence for commercial projects. For our crew, each construction job is a brand-new adventure. For more information on organizing a building project, get in touch with Level X Construction! We are happy to build you.